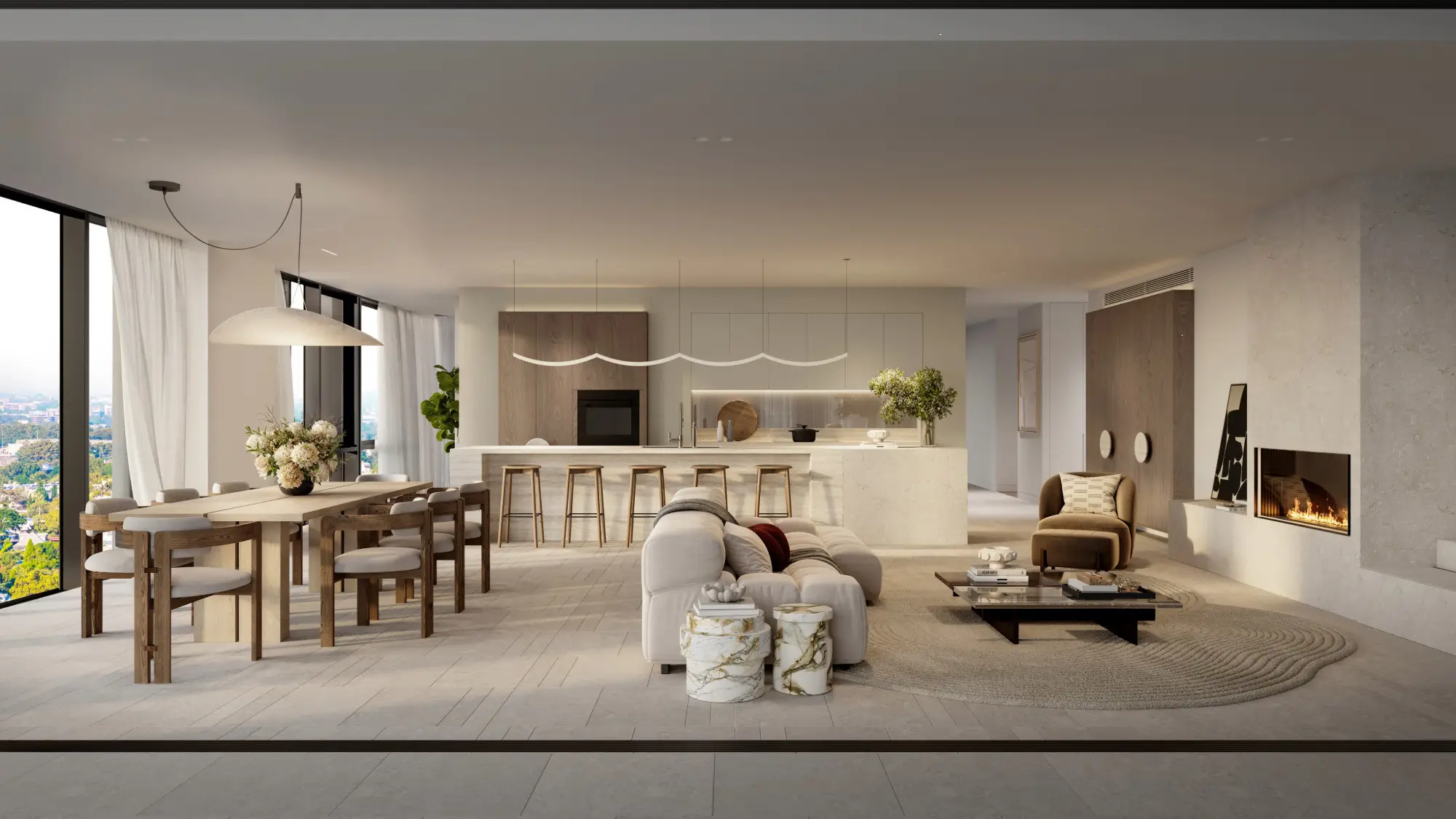
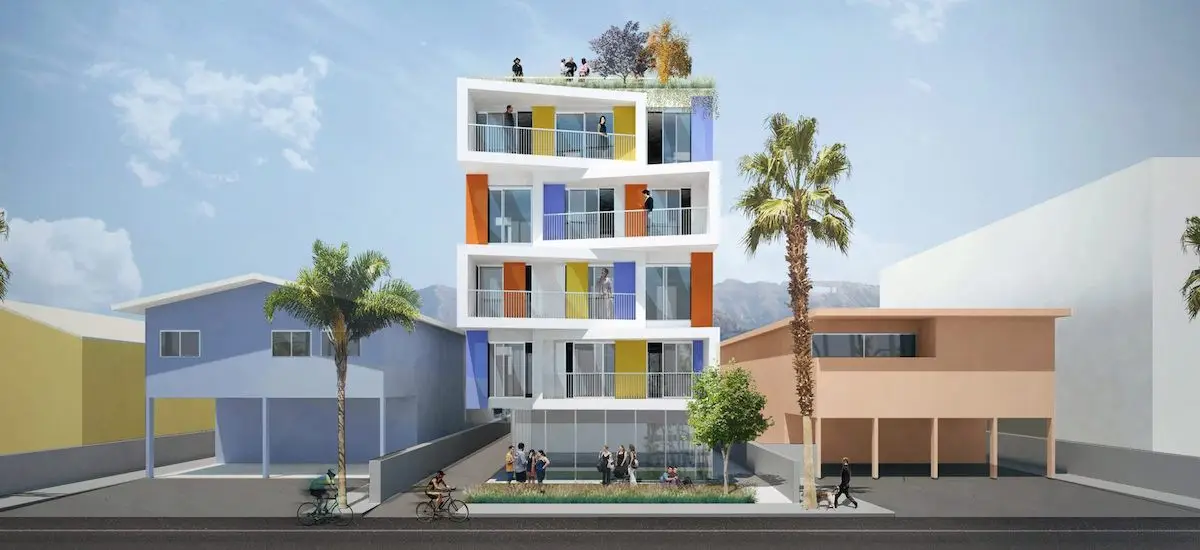
Affordable housing is no small issue in Australia, but a prefabricated, modular unit concept by California firms Brooks + Scarpa and Plant Prefab may have the solution.
A concept that can be arranged in various configurations and envisioned for vacant or underutilised land plots, the Nest LivingHome system was initially created in response to the dramatic rise in housing costs and homelessness in Los Angeles and the USA.
Made up of stackable, prefabricated units, the design is meant to offer a cost-effective and high-quality solution to social housing — in particular for those people who live on the streets.
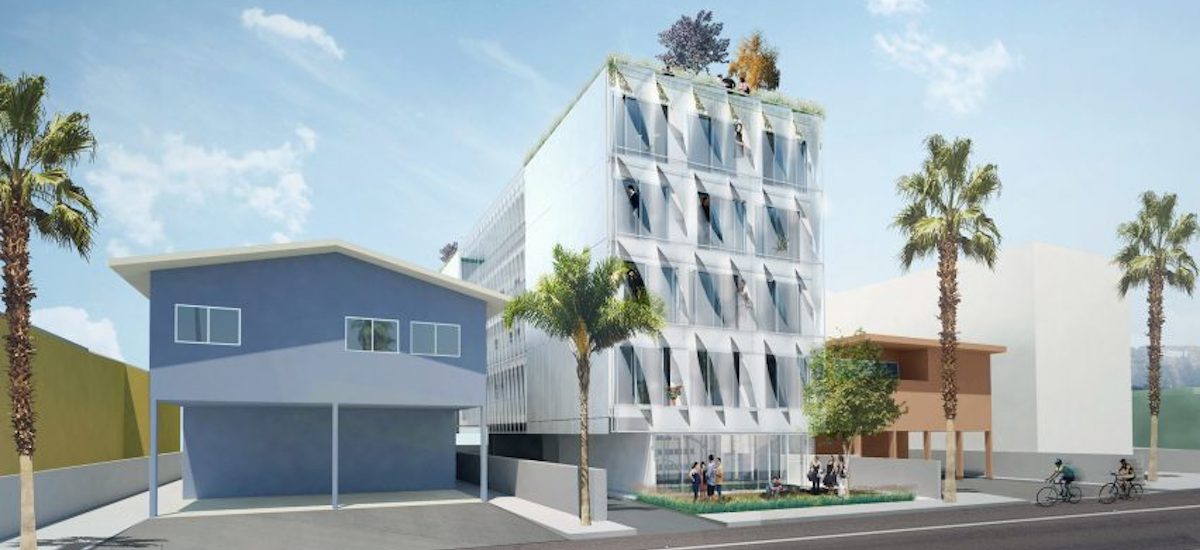
“A main goal for the concept was to give homeless people a sense of dignity and shared social spaces,” a spokesperson at Brooks + Scarpa said.
The Nest system comprises of modular units that can be assembled like a kit of parts. These can then be put together in different configurations to suit the land it is occupying. Not only this, it can reach up to five storeys high.
Inside, the modules can also be changed to fit the clients specific brief, making the system particularly well suited for homeless shelters and single-room occupancy buildings, in which tenants rent a simple bedroom. However, the design can also be used for apartment buildings with a more traditional style.
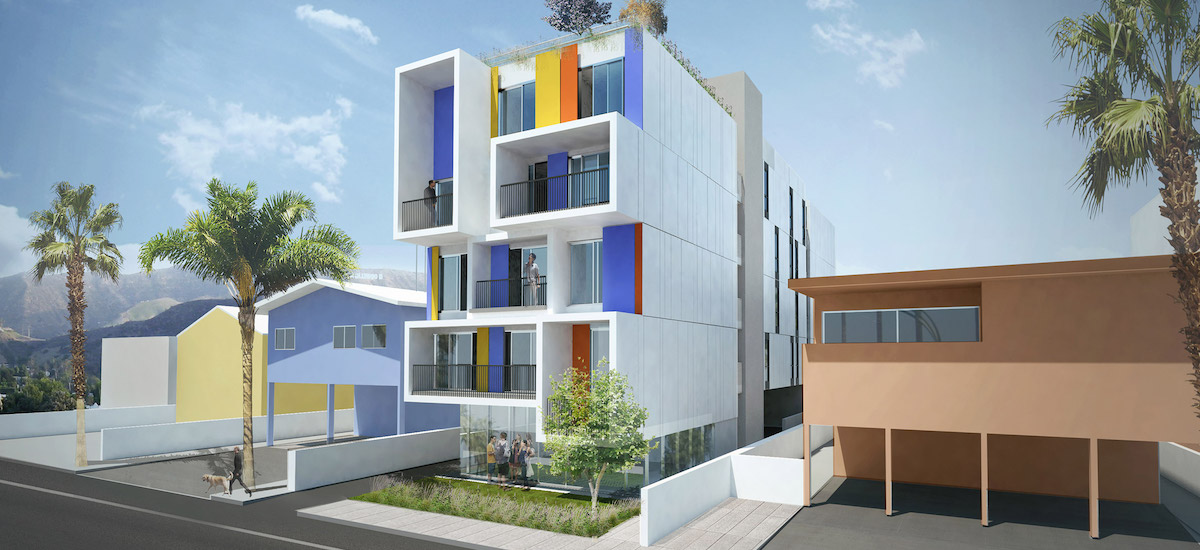
"Like the nesting habits of birds, the toolkit is based on the different ways people live with the objective of giving everyone an affordable place to live," said Angie Brooks, managing principal at Brooks + Scarpa.
The team have conveyed three different models, each named after bird species. One, called Bluejay, serves as a temporary shelter that can hold up to 224 people.
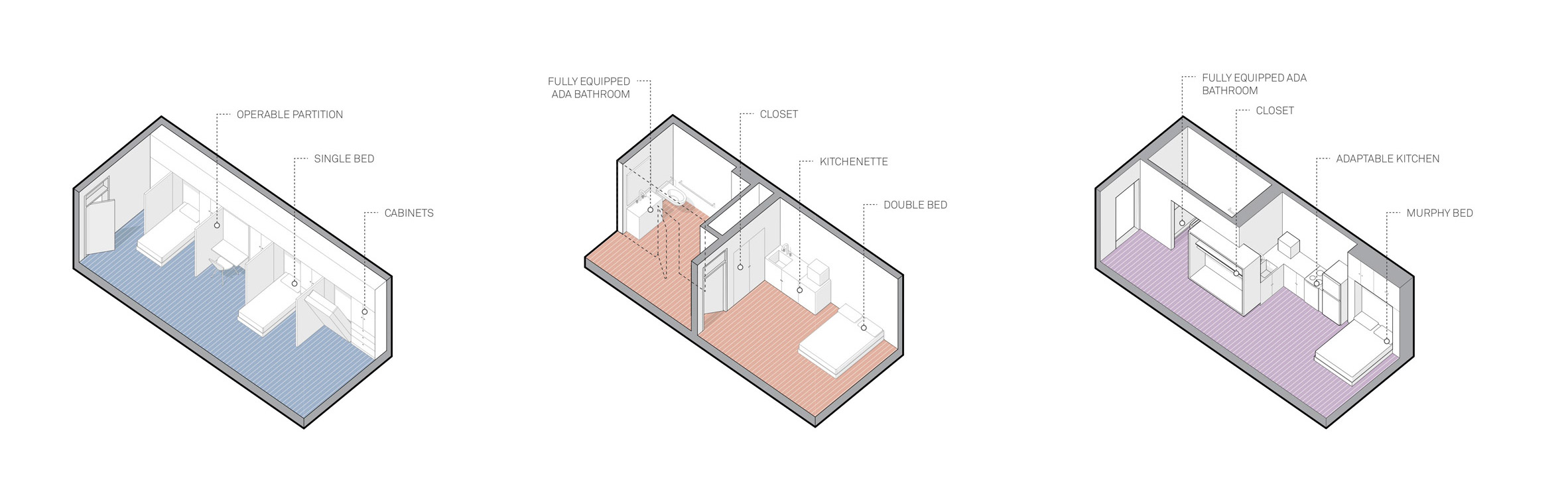
Another model, named Dove, is curated as a more permanent housing system with support services. It features communal spaces and up to 48 bedrooms. Meanwhile, the third option, Osprey, is presented in a similar mould and contains studio, one or two bedroom apartments, along with private kitchens and bathrooms.
The structure would be made up of wooden load-bearing frames, in conjunction with a metal or cement-board siding. The exterior and interior finishes can be customised, including the colourful façade panels. A rooftop garden can even be incorporated, particularly if open space is limited at ground level.
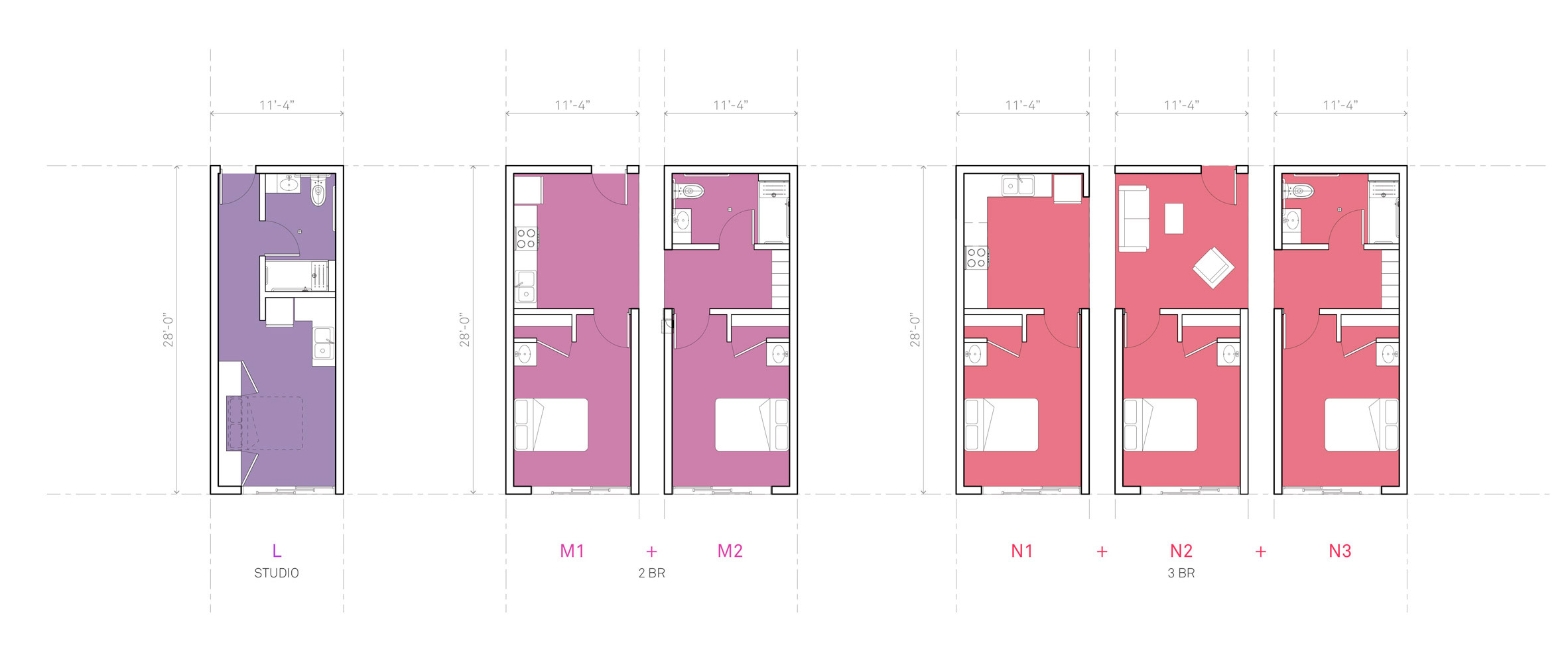
The structures would be constructed in Plant Prefab's factory, cutting the build time in half and significantly reducing costs.
“We know that people are frustrated by the slow pace of solutions for affordable housing,” said company founder and CEO Steve Glenn. “Prefab construction can help increase the pace.”
In 2018, the team at Brooks + Scarpa won a $1 million (USD) grant from LA County as part of its Housing Innovation Challenge. As a result, the Nest toolkit is expected to be utilised for an upcoming housing project in Santa Monica, California.
In Australia, one of the country’s biggest banks, NAB, has recently made a mammoth $2 billion (AUD) pledge to support affordable and social housing initiatives over the next three years.
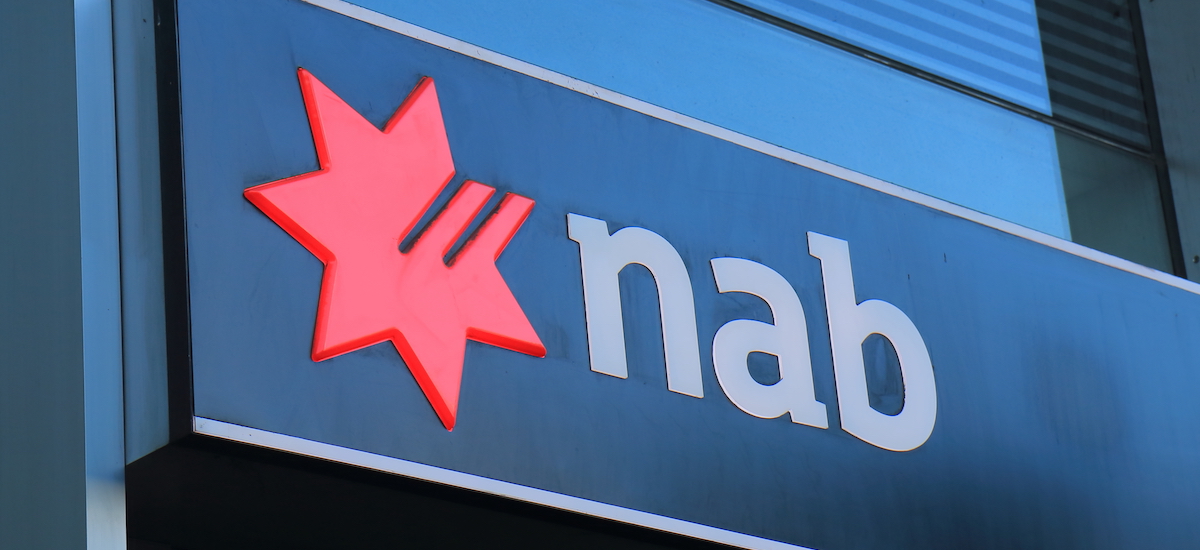
Modelling undertaken by the University of New South Wales predicts an affordable and social housing shortfall of one million dwellings by 2036 — and NAB is planning to limit these numbers.
One of the groups to benefit from NAB’s initiative is Launch Housing, one of Victoria’s largest homelessness and housing support service providers.
By June next year, the not-for-profit will have completed 57 innovative “tiny homes” as part of a groundbreaking approach to creating affordable accommodation for at-risk people.

The low-cost, rapidly-built compact dwelling follows a similar business model to that of Nest LivingHome’s, but will others follow more of a “flat-pack” building-style? The success of the project in LA has a large part to play in that answer.
Click here to read about the social housing project that claimed the Stirling Prize in the UK.